深海盛开“海葵花”
探访亚洲首艘圆筒型浮式生产储卸油装置
中央纪委国家监委网站 王珍 通讯员 牟银滔
“海葵一号”浮装作业现场。
工作人员对“海葵一号”内部进行安全检查。
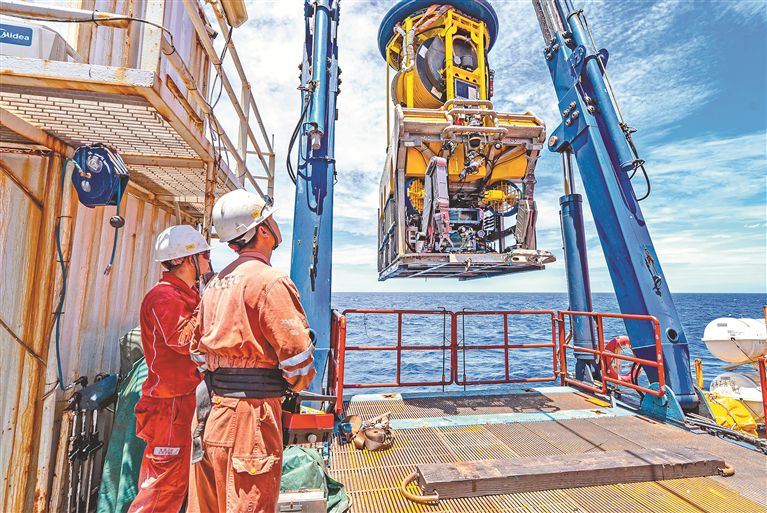
水下机器人即将入水开展作业。
作业人员进行“海葵一号”锚缆回接挂扣。
扎根深海的“海葵一号”与“海基二号”导管架平台遥遥相望,投产后将共同服役于流花油田。 中国海油深圳分公司 供图
南海深处,在距离深圳东南约240公里的流花油田海域,“海葵一号”如同一朵盛开的葵花绽放于深海之上,与亚洲第一深水导管架平台“海基二号”遥遥相望。
“海葵一号”,我国自主设计建造的亚洲首艘圆筒型FPSO(浮式生产储卸油装置),是集原油生产、储存、外输等功能于一体的高端海洋装备,由近60万个零部件组成,总重近3.7万吨,相当于3万辆小汽车,最大直径约90米,高度接近30层楼,主甲板面积相当于13个标准篮球场,最大储油量达6万吨,每天能处理约5600吨原油。
从一纸方案到建造完成,再到海上安家,这一国之重器有何与众不同、经历了哪些“千锤百炼”?又将如何服务于深水油气开发?我们一起走近“海葵一号”。
锻造重器——
创下建造周期最短的世界纪录
随着世界海洋油气开发向深远海发展,铺设长距离油气管道的成本越来越高、风险也越来越大。解决这一难题最有效的途径,就是在海上建设FPSO。
FPSO是集油气生产、储存、外输于一体的“海上油气加工厂”。目前,我国已成为全球最大的FPSO制造与应用国之一,所拥有的FPSO数量与总吨位均居世界前列,自北向南分布于我国广袤海域中,支撑着我国海洋石油近80%的产能。
以往,我国的FPSO主要是船型结构,为什么要把“海葵一号”设计成圆筒型呢?“相对传统的船型,圆筒型体型更小,空间更紧凑,储油效率明显提高,并具有抵御恶劣海况能力强、钢材用量少、经济适用性高等显著优势。国际上此前共有6艘圆筒型FPSO,‘海葵一号’是首艘应用于亚洲海域的圆筒型FPSO。”中国海油深圳分公司流花油田开发项目副总经理王火平介绍说,“而且圆筒型FPSO不需要复杂的单点系泊系统,相比船型FPSO可回接的管缆数量更多,更小吨位即可实现安全作业要求,是将来深水油气开发装备的重要发展方向。”
历经近十年的研究和设计,2022年3月,“海葵一号”在青岛开工。顾名思义,圆筒型FPSO拥有大直径的圆柱形筒身,船体内可储存原油,船体甲板上方搭载生活楼、处理设施、发电设施、外输系统等。其生产工艺和整体构造非常复杂,在相当程度上体现了一个国家的海洋工程综合实力。它究竟是怎么一步步建造起来的呢?
“海葵一号”设计经理冯丽梅告诉记者,第一步是将近60万个零部件,组装成123个船体分段和8个上部模块;第二步是将所有分段进行合拢,完成船体建造;第三步是将上部模块和船体进行总装集成,实现整体功能融为一体;第四步是对60个大系统、310个子系统进行联合调试,使“海葵一号”具备完工交付条件。
“海葵一号”在数字化智能化、绿色低碳环保等方面应用了先进的设计理念,其自主化、国产化水平都实现了重要突破。“我们自主研制海陆一体化智能中控系统,在台风来临时可切换到智能模式,实现无人化生产,为海上油田的智能化建设提供一种全新模式。同时,国内首次在海洋平台采用新型天然气脱硫装置和双燃料发电机,可以充分利用油田伴生气,有效提升了项目的绿色节能水平。大容量液压潜没泵等一系列关键装备也都实现了国产化。”冯丽梅说。
2024年4月26日,“海葵一号”在青岛建造完工。几天后,开始离港、起运,一路向南,踏上1300多海里的征途。这是众人翘首以盼的时刻,不少为之付出心血的人早早来到码头,目送其远去。
“海葵一号”历时两年的建造周期,较国际同类型装备缩短了近一半,创造了建造周期最短的世界纪录。
水下“接龙”——
精准回接让“海葵一号”在深海站稳脚跟
6月1日,王火平登上“海葵一号”已经10天了,一直饱受南海内波流、大风、暴雨等复杂海况的困扰。作为海上安装作业的负责人,他正与现场170多名工程师和工人致力于锚缆的回接作业。
据了解,未加固定的浮式生产装备像是“无根浮萍”,受洋流影响四处运动无法正常工作。“‘海葵一号’要在海上开采油气,首先要在深海站稳脚跟,锚缆回接是其中的关键环节。”王火平介绍。
简单来说,锚缆回接就是将之前预铺设在海底的锚腿与“海葵一号”上布设的牵引链连接起来,从而将“海葵一号”牢牢固定在设计位置。然而,看起来简单的系泊安装背后,却涉及复杂设计计算、装备技术能力、恶劣海况施工等多重技术挑战,是世界级海洋工程难题之一。
“这是国内首次对圆筒型海洋装备进行海上安装,由于圆筒型结构重心高、稳定性差,很容易发生旋转,我们采用多点系泊形式,使用12根分别长达2570米的高强度系泊缆,从东北、东南、西北三个方向提供稳定的系泊力,将‘海葵一号’牢牢固定在海底。”王火平说,“海葵一号”采用国内入泥最深、系泊载荷最大的吸力锚,每根锚缆能承受高达2300吨的拉力,相当于1500多辆小轿车的重量,即便遭遇百年一遇的恶劣海况也可以稳稳扎根海床上。
彼时,“海葵一号”正被三艘拖轮从三个方向拖拽着,形成稳定的三角形结构,进行精准定位。主作业船“海洋石油291”位于两艘拖轮之间,甲板上,施工团队忙而有序地在轰鸣的机器中穿梭,所有人的注意力都在这场“抢时赛”上。
“工程所在海域水深达324米,风向多变、海况复杂,对施工技术要求极高。”守在船上的资深工程师王德洋对记者说,“作业过程可以形象地比喻为水下‘接龙’,回接前首先要将‘拴马桩’一样的吸力锚,穿过324米的海水打入海床以下21米,确保牢固扎根。回接时需要操作水下机器人,在阳光都照不到的海底进行精准作业,作业过程受强对流天气和南海内波流等叠加影响,对安装技术提出了极大挑战。”
与甲板的喧嚣不同,水下机器人控制室内静得能听到呼吸声。监控屏幕上展示着300多米深的海底情况,“水下机器人监督”崔相鲁带领团队操纵着机器人在波涛汹涌的大海里“穿针引线”。在水下机器人的“协助”下,施工团队将提前铺设在海底的锚链逐根捞起,并与“海葵一号”上预留的牵引链进行“接龙”。
6月2日上午,首根锚缆回接成功!这给现场工程师们注入了一剂强心针。“这证实锚缆的回接方案非常有效。”王火平说,但他们不敢有丝毫松懈。
6月10日中午,随着最后一根系泊锚缆牢牢地锁紧固定,“海葵一号”锚缆回接作业顺利完成,12根锚缆像12条巨龙般将这一巨型“海上油气加工厂”牢牢固定在深海,作业效率和回接精度均达到国际先进水平。
“以柔克刚”——
为深水装备穿上“中国装”
圆筒型FPSO吃水小,尺度和受载面积大,环境载荷是同等吨位船型FPSO的2倍以上,系泊缆张力较大。若采用常规FPSO的“锚链-钢缆”系泊方式,“海葵一号”需要21根系泊缆。但实际上,“海葵一号”仅使用了12根锚缆。其背后奥秘是,创新采用了更“软”的系泊材质。
据介绍,“海葵一号”的锚腿由多段锚链、聚酯缆连接而成。其中,聚酯缆以高强聚酯涤纶绳为内芯,外部编织耐磨涤纶外套,10万多根纤维组成一根整绳,直径仅274毫米。相比传统钢缆,聚酯缆重量轻、成本低,且耐腐蚀、强度高,在受力时可产生一定的弹性变形,有利于缓解和吸收波浪耦合作用,达到“以柔克刚”的效果。
“全部12条锚链和4条聚酯缆均为国产锚链和国产聚酯缆的首次规模化应用,有效推动了我国深海锚泊系统设计、制造和安装技术取得全方位突破。”王火平介绍。
不仅如此,“海葵一号”按100年一遇超强台风工况设计,高度集成了超700台关键设备,这些设备中约九成都是由我国自主设计制造的。其中,我国自研的中控系统、海洋一体化监测系统等技术和设备,均为在圆筒型FPSO上的首次应用,实现了关键设备自主研发应用的重要突破。
2.5公里外,早已在此矗立的亚洲第一深水导管架平台“海基二号”全程见证着这位新伙伴“上岗”。据介绍,“海基二号”的总高度达428米,总重量超5万吨,刷新海上原油生产平台高度和重量两项亚洲纪录,共设生产井24口,搭载了原油工艺和外输系统、生产水处理系统及电力供应系统等300余套设备,可实现远程水下井口控制、智能油气开采、台风生产模式等功能。
后续,“海葵一号”将与“海基二号”平台陆续开展联合调试等工作,投产后一起服役于我国第一个深水油田——流花油田的二次开发项目,创新形成“深水导管架平台+圆筒型FPSO”开发模式。与以往深水油气田采用的水下生产系统开发模式相比,其采收率大幅提高,可将油田生产寿命延长近30年,同时却能大幅降低开发成本,为我国深水油气田开发提供了一种新模式。
“‘海葵一号’、‘海基二号’两座设施均创亚洲纪录,攻克了圆筒型浮式生产装备一体化系统、超大型海洋平台轻量化设计等系列技术难题,形成了两项世界首创、十余项国内首创技术,工程建设整体达到世界先进水平。”王火平说。
中国海油深圳分公司流花油田总经理江俊达表示,流花油田位于南海深水区,由于其特殊的地理位置,每年受台风影响关停时间超过7天,造成原油产量损失超过8万吨。依托“海葵一号”、“海基二号”,中国海油首次在深水油田新项目中采用台风无人生产工艺,可在陆地远程操控生产,具备极端工况下的安全关停、海管置换、恢复生产等功能,极大地保障台风期间油田安全平稳运行。
据悉,我国300米以上的深水区域蕴藏着丰富的油气资源,逐渐成为海洋油气开发的重要战场。近年来,中国海油依托重大工程项目,牵头联合国内知名高校、科研院所和企业,采取“产、学、研、用”相结合、工程项目与科研项目紧密结合的科技创新模式,突破了一系列关键技术,全类型深水油气装备自主建设能力得到大幅提升。
中国企业新闻网摘编:亓淦玉 |